山東埃爾派 | 點擊量:0次 | 2021-02-07
高爐渣
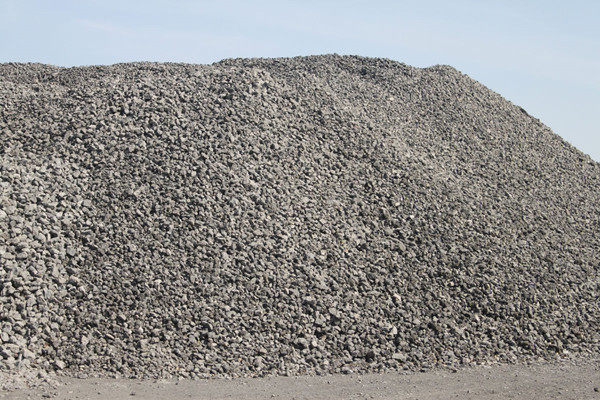
高爐渣是什么 高爐渣顯熱回收方法有哪些
鋼鐵企業(yè)余熱資源主要集中在煉焦、燒結、煉鐵、煉鋼和熱軋工序,表現為產品余熱、煙(煤)氣余熱、廢渣顯熱及冷卻水顯熱等。鋼鐵企業(yè)各類余熱資源中,產品及煙(煤)氣顯熱占余熱資源總量較多,余熱品質包含各個溫度等級。目前已開發(fā)并應用的技術有干熄焦技術、燒結余熱回收技術、轉爐煙氣余熱回收技術、連鑄坯熱送熱裝技術等等,取得明顯效果和效益。冷卻水顯熱雖然也占一定比例,但屬低溫余熱資源,回收經濟效果較差,余熱回收率僅2%左右。爐渣顯熱能級高,屬高品位余熱資源,約占全部高溫余熱資源的35%,其中高爐渣占28%,回收價值很大。但是由于回收技術上的困難,目前渣顯熱回收率極低,只有部分高爐渣沖渣水余熱得以利用,高爐渣顯熱是少數還未被開發(fā)利用的重要余熱資源。
高爐渣的出爐溫度在1400~1550℃之間。每噸渣含(1260~1880)×103kJ的顯熱,相當于60kg標準煤的熱值。高爐渣的排出率與礦石品位有關,近年來我國大中型鋼鐵企業(yè)采用較高品位鐵礦石原料,高爐渣鐵比已降至300kg/t附近。由此,一座1000m3的高爐,按年產量90萬t生鐵、渣鐵比為300kg/t計算,每年排渣量27萬t,爐渣放散熱量折合標煤1.62萬t。據不完全統(tǒng)計,我國已經投產和在建的1000m3級以上的大型高爐約有169座,估算綜合生鐵產能在3.2億t左右,因此每年我國大型高爐產渣量接近1億t,攜帶熱量折合標煤600萬t。而實際生鐵產量和渣鐵比都高于計算值,因而高爐渣顯熱能量更為巨大。盡管并非可以全部回收高爐渣的熱能,但若能部分回收利用,其節(jié)能效益也是顯著的,非常具有市場開發(fā)潛力。
高爐熔渣是在高爐煉鐵過程中,由礦石中的脈石、燃料中的灰分和溶劑(一般是石灰石)中的非揮發(fā)組分形成的固體廢物。主要含有鈣、硅、鋁、鎂、鐵的氧化物和少量硫化物。是高爐生產的主要副產品,主要成分為CaO、SiO2、Al2O3、Fe2O3、MgO、TiO2等,含有大量的高品質熱焓,具有很高的回收價值。
高爐渣顯熱進行回收,需要解決兩個主要問題:一是對高爐熔渣進行?;菬崃康幕厥?。水淬?;荒芑厥诊@熱,干式?;幚砗罂梢赃M行顯熱回收。熔渣顯熱回收技術主要有物理熱回收技術和化學熱回收技術兩類。
各種物理熱回收方法,都需要借助于一定的載能體(空氣等)來回收熔渣的顯熱,綜合熱回收效率不高?;瘜W法回收熔渣顯熱不僅可以省去眾多余熱回收設備,且由于能量形式轉換次數少,回收率高,受到廣泛關注。日本科研人員在這方面做了大量工作,主要有以下形式:
1、甲烷循環(huán)反應
流程為:
1)利用高速噴出的甲烷(CH4)和水蒸氣(H2O)混合氣體對液渣進行冷卻?;?,二者進行強烈的熱交換。液渣受到風力的破碎和強制的冷卻作用,其溫度迅速下降并?;癁榧毿☆w粒。
2)CH4和H2O的混合氣體在高爐渣顯熱的作用下,發(fā)生吸熱反應生成H2和CO,將高爐渣的熱量轉移出來;
3)生成的氣體進入下一反應器,在一定條件下,H2和CO反應生成甲烷和水蒸氣,放出熱量。高溫甲烷和水蒸氣經熱交換器冷卻,重新返回循環(huán)使用。
2、甲烷-水蒸氣重整制氫
流程:
1) 用轉杯?;夹g對熔渣進行粒化,采用CH4和H2O氣體作為冷卻介質。
2) 氣體吸收化學顯熱,在催化劑作用下,生成H2和CO氣體。
3、沼氣-二氧化碳重整制氫
反應為CH4+CO2=2CO+2H2。消耗能量247kJ/mol,來源于熔渣顯熱。研究表明:渣粒不僅起到提供熱量的作用,且是一種很好的催化劑,能促進甲烷的分解;隨著反應溫度的升高,甲烷的轉化率增大,最高達96%左右,且生成更多的氫氣。
4、利用爐渣顯熱制煤氣
高爐熔渣在處理過程需要急速冷卻;而煤的氣化需要不斷加熱、升溫,因此可以將兩者結合起來,目前,我國學者正在進行這方面的研究。
5、高溫熔渣直接制備材料
利用高溫熔渣直接制備高附加值材料,對熔渣進行調質,直接熱成型為礦棉、微晶玻璃等高附加值材料。這樣做間接回收了熔渣顯熱,避免了傳統(tǒng)水淬工藝帶來的問題,簡約了熔渣資源化的流程。然而,熱成型后的產品仍蘊含較高的顯熱,仍被浪費。與上述幾種方法相比,熱量回收的不夠徹底。
綜上,高爐渣是一種很好的二次資源,水淬法不可以回收顯熱,而化學法則可最大程度回收利用這類特殊資源。多種化學法中,甲烷PCA和重整最為受人關注,即回收了熔渣顯熱、減少了污染物排放,同時生產的氣體可以直接用于高爐煉鐵生產,實現循環(huán)經濟,是高爐熔渣顯熱回收的最好方式。
上一篇: 粉煤灰微珠
下一篇: 氧化鋅